After the accidents in the boiling water reactors in Fukushima Dai-ichi on March 11th 2011, reliable decay heat removal became a main part of the reactor safety research. Since that accident new concepts for a decay heat removal system have been developed.
In the frame of the sCO2-QA project (Qualification of analysis tools for the evaluation of residual heat-driven, self-sufficient system for decay heat removal), a residual heat-driven self-sufficient sCO2-operated decay heat removal system, based on a Brayton cycle, shall be simulated by a numerical model. For the validation of this model and the design of the components (heat exchanger, turbokompressorsystem, etc.), experimental data are needed. The model will be implemented in the German numerical code ATHLET (Analysis of thermal-hydraulics of leaks and transients). Furthermore, the experimental results will be used for validation and/or improvement of heat transfer and pressure drop correlations for the working fluid sCO2.
To be able to understand the heat transfer characteristics of sCO2 in the critical region and to simulate these in complex structures like heat exchanger, it is necessary to consider simple geometries like a single channel first. On this occasion, a new test rig for fundamental investigations of the heat transfer characteristics and pressure losses of sCO2 near the critical point was build up at IKE. The experiments are running on in the test facility SCARLETT (Supercritical Carbondioxide Loop at IKE Stuttgart) at the IKE (Institute of Nuclear Technology and Energy Systems), which provides sCO2 under defined conditions.
Schematic of the sCO2-QA test rig, 2018 © Theologou, IKE
The test rig consists of three tubular test sections with different tube diameters. It is variably mounted on a rack allowing for experiments with horizontal, upward and downward mass flows. The first and the second test section have the same structure, the only difference is the inner diameter of the used test tubes (4 mm and 8 mm). The third test section is used for investigations of pressure losses. The test tubes are heated up directly with a DC power supply. Before the sCO2 passes the test tubes the mass flows and the bulk temperatures are measured. The total length of the first test tube is 2360 mm with a heated length of 1640 mm. The second test tube is 2500 mm long with a heated length of 2040 mm.To calculate the local heat transfer coefficient, resistance temperature sensors are tied on the outer surface of the test tubes.
Foto of the sCO2-QA test rig, 2018 © Theologou, IKE
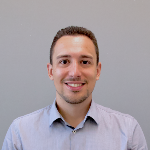
Konstantinos Theologou
M.Sc.Research Associate / Doctoral Candidate